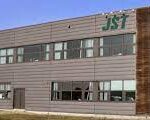
Customer Success Story: JST France SAS
March 18, 2021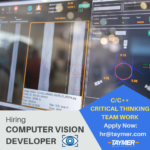
Computer Vision Developer – USA – Texas
November 7, 2022Innovation in Inline Defect Detection for Profiles | Taymer International Inc.
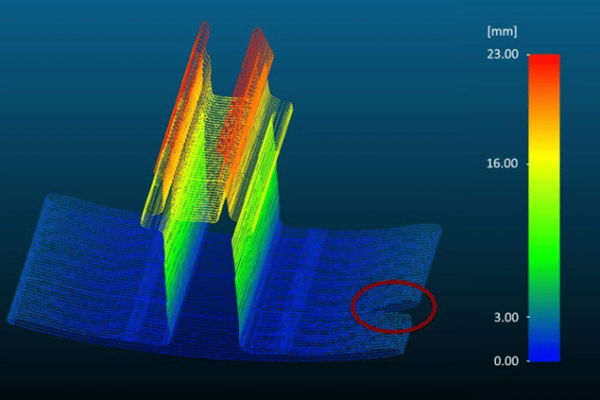
New Innovation for Inline Defect Detection with Taymer Technology
Over the last year, Taymer has continued to step out of its comfort zone to bring innovative solutions to challenging new applications. Our vision technology is continuously developing to satisfy the increasing demands of our growing global customer base.
Laser Profiling with Camera Surface Inspection
The coupling of Taymer’s traditional camera inspection technology with laser profiling brings you surface and dimensional defect detection on extruded profiles – all in one unit.
On a traditional camera system, the complete view of a profile’s feature can potentially be obstructed by the profile itself. For example, another feature on the profile would prevent the system from inspecting and giving a dimensional measurement of the original feature. For a defined type of profile, one solution is to place the cameras in specific positions to optimize their individual field of view. Giving each axis of inspection a range of adjustability will also help make the inspection machine more modular as a whole. It’s more adaptable to other profile types and even to potential future products.
One problem remains however, cameras give flat 2D pictures. While we can see the product and judge every pixel to understand a defect and its source, we don’t have a 3D understanding of the distance between certain points of a feature.
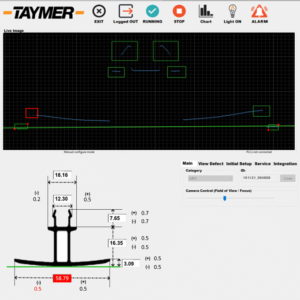
To solve this problem, Taymer now leverages the power of laser technology.
On the top half of the user interface seen on the left, the acquired data from one laser is displayed in real-time. On the bottom half of the interface, several measurements of the profile are indicated on a diagram of the part’s cross-section.
Live calculated measurements are displayed inside the text boxes. The specifications for each tolerance are shown on the diagram. In the event that a measurement falls outside the desired tolerance, the faulty dimension will be highlighted on both the live image and the cross-sectional diagram by a red box.
To support this useful information, a live 3D render of your profile is also available in the user interface. This will give you a better visual representation of the product being inspected and the identification of any defects.
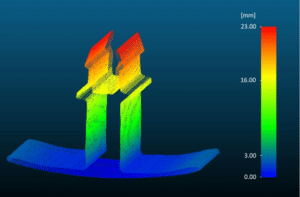
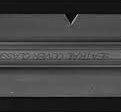
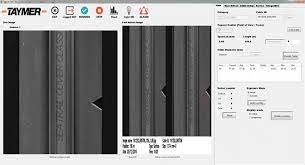
As the laser moves over the defective portion of the profile, the width is measured and compared to the desired specification. As it falls outside the acceptable tolerance, the software alarm is triggered. The defect is detected by the surface inspection system (top) and the laser profiler (bottom). The alarm message is displayed, the defect data saved, and the defect counter is incremented.
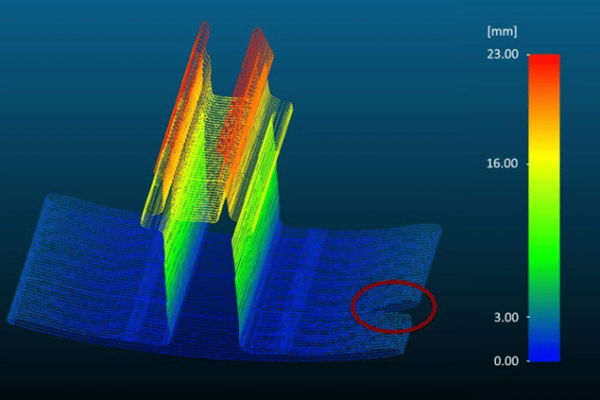
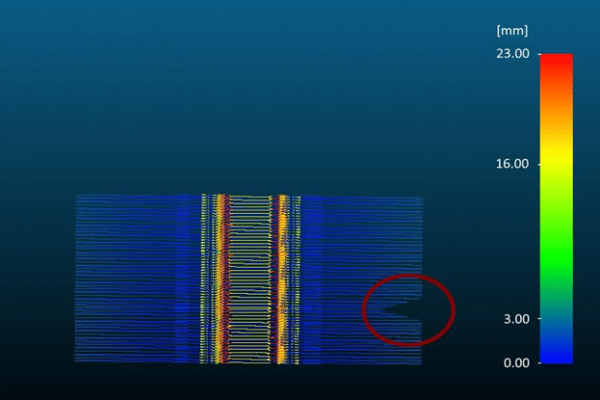
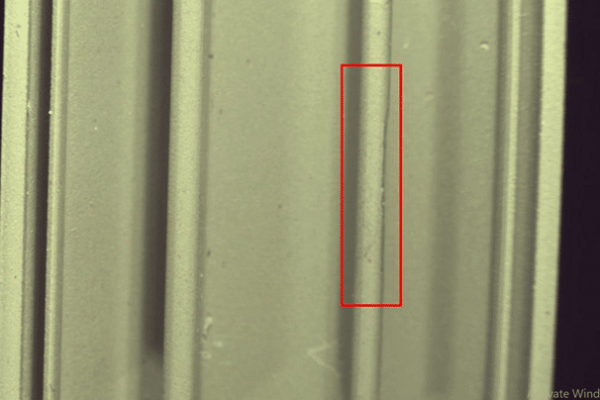
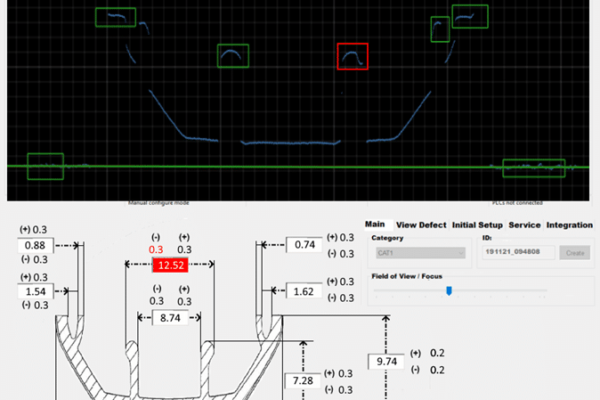
As you can see in the red rectangle, the profile is visibly distorted at the edge. Again, the defect is detected by both the surface inspection system and the laser profiler. The operator is readily informed of the situation by getting immediate feedback on both screens via the diagram and the photos.
The defect is saved into the system and the data included in the reporting. The SI4100-LP can be fully integrated into your production line, exchanging information with other machinery via your line control systems. This will allow you to take corrective action on the fly and reduce any scraps and reworks.
Even when restricted to using just one laser, the live render seen on the left underlines the huge benefit of being able to look at a defect from two vantage points simultaneously.
The several visible gaps in the 3D model are due to the fact that the laser profiler scanned the sample from a top-down viewpoint. Even with these gaps the 3D model clearly displays the simulated defect. This area is highlighted by a red circle.
Taymer’s combined SI + Laser system is able to provide both images of defects detected by the laser, as well as adding a second layer of inspection for types of defects that may not be caught by laser profilers such as discolorations. Utilization of the SI + Laser system allows customers to inspect 100% of their product for both visual and profile imperfections, providing a level of quality assurance previously unattainable.