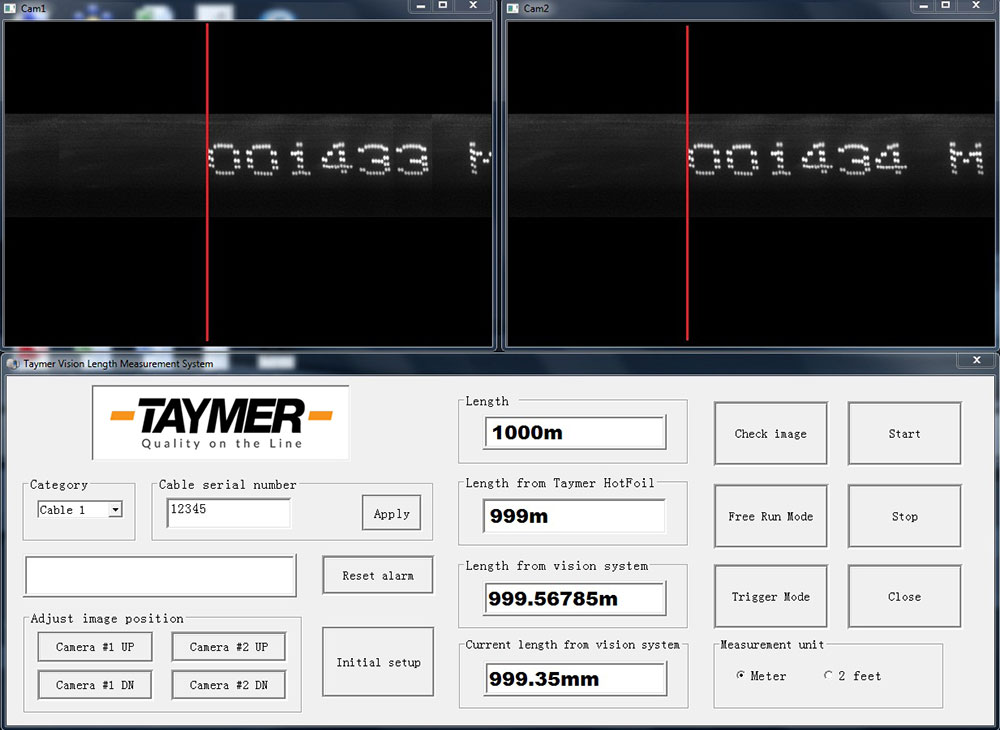
IWCS 2016 – Print Length Verification for Cable
October 6, 2016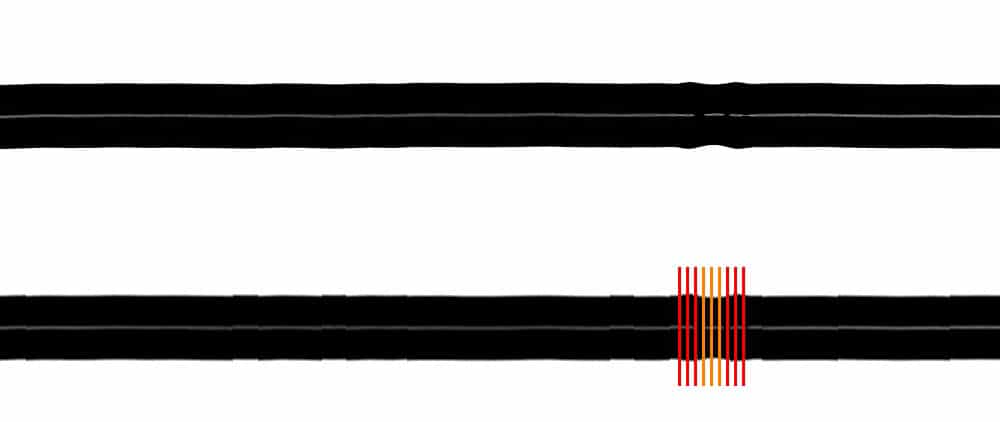
IWCS 2018 – High Speed Lump and Neck-down Detection with Accurate Diameter Measurement
November 10, 2018IWCS 2017 – Fiber Ribbon Dimensional Measurement and Color Sequence Verification
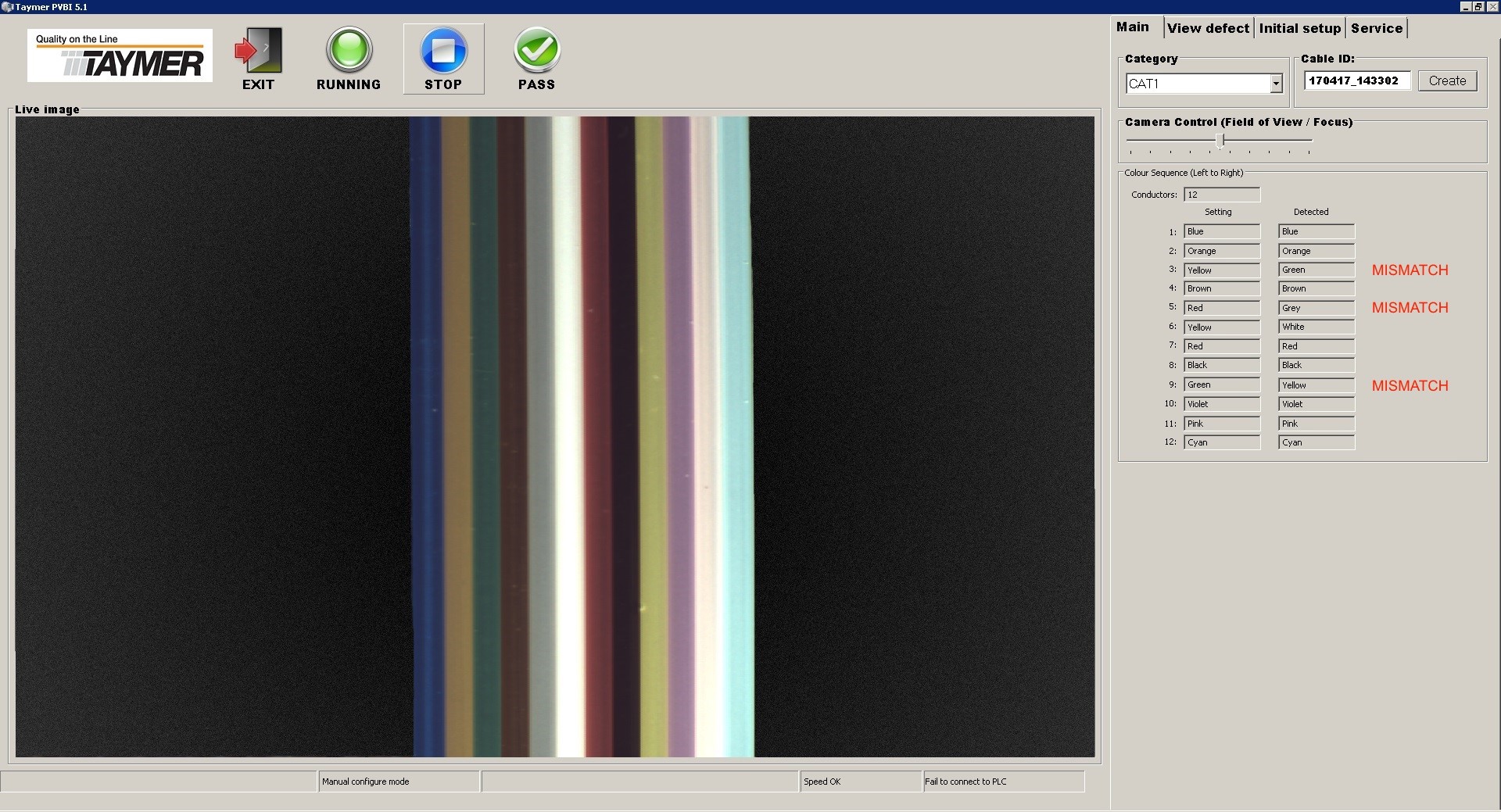
Figure 3. Detected Incorrect Ribbon Color Sequence
Fiber Ribbon Dimensional Measurement and Color Sequence Verification
Mr. Craig Girdwood, Mr. Andrew McCloskey
Taymer International Inc., Markham, Ontario, Canada, +1-905-479-2614
Abstract
Taymer’s fiber Ribbon Inspection system (RI) is a tool that allows fiber optic cable manufacturers to improve quality of their fiber optic ribbon production process. Fiber optic ribbon is increasing in popularity in the United States and other countries as a method of grouping different fiber strands together. Ribbon cable needs to have consistent geometry to tightly stack multiple ribbons with the high fiber density that is one of the ribbons primary benefits. As ribbon production is a very high speed process, this Ribbon Inspection system is the only way to ensure that the geometry of the ribbon is correct without creating hundreds or thousands of meters of poor quality ribbon.
Introduction
Ribbon optic fiber constructions are becoming more common, in the USA and other countries, displacing loose tube applications. Ribbon has several advantages over loose tube fiber, including easier splicing, smaller footprint and higher fiber density. These benefits require that the fiber ribbons are able to be packed tightly and consistently along the whole length of the cable and the fiber does not change order within the ribbon.
Ribbon manufacturing process is typically a high speed process, with lines running above 500 meters a minute. Taymer’s Ribbon Inspection technology is the only inspection system specifically designed to inspect fiber optic ribbons for geometry defects including the ribbon width, thickness, planarity and gap between fibers.
The Ribbon Inspection system has been designed to not only inspect the geometry of the fiber ribbon, but to also check the sequence of fibers within the ribbon. The fibers in the ribbon are individually colored and it is critical that the color sequence is consistent along the length of the ribbon. The RI system can be setup to compare the current color sequence of fibers to a preset template. Changes in the ribbon color sequence can be automatically detected by the system software. This color inspection technology has the added benefit of also measuring changes in the fiber color, or even if the color of the fiber is missing.
The fiber Ribbon Inspection system is able to be easily integrated into existing or new production lines, and is designed to cover a large range of ribbon fiber counts. The Ribbon Inspection system makes sure that the ribbon dimensions and color sequence is correct, and consistent for the whole run before further processing occurs resulting in poor quality cable.
The lifetime of the lights and pulleys can be over 50,000 hours of usage and they are the only consumable parts.
Previous Ribbon Inspection Limitations
Manual Inspection
The standard procedure for checking dimensionality and color sequence of fiber ribbon during production is to cut off a small section of the start of the run. The ends are then inspected using a microscope to check the quality of the ribbon geometry and the color sequence is correct. The microscope is essential due to the tight tolerances requirements of today’s ribbon manufacturing. With this method if the ribbon quality at the start of the run is poor, the run can be halted and corrective action is taken before the run properly begins. The manual inspection does not provide a way to check if a defect occurs during a run until the whole run is complete.
Laser Inspection Gauge
A laser gauge is the most common method of inspecting round profiled cables. This technology is simple to produce the overall diameter of the product, which is the main dimension that is required to be measured. The relatively complex assembly of the ribbon and accuracy required for fiber ribbon manufacturing prevents laser from being used as a reliable way to check ribbon dimensionality. Laser is also unable to inspect color sequence to detect if a fiber strand changed locations during a run.
Machine Vision Inspection System
Optical Mechanical Design
The Ribbon Inspector utilizes three high speed cameras to capture images of the ribbon. Two of these cameras inspect the ribbon geometry and one high speed color camera to capture images of the color sequence. The cameras are orientated orthogonal to the ribbon surface. One of the two cameras is used to inspect the top surface geometry, and the other camera inspects the bottom surface geometry. The data is combined from both cameras to determine the overall ribbon geometry.
The third camera is a color camera operating at high capture rates, to continuously measure the colors of the individual fibers. The correct color values are preset into the system, so if the sequence of the colors sequence changes during a run the software will flag this as a defect. The software can be configured to also check the color quality of the individual fibers in the ribbon, allowing the system to detect if color is missing from the fiber or the hue changes significantly.
The system operates in-line using customized guiding and lighting to provide 100% coverage of the ribbon geometry along the whole length of the run. The system has been designed for high speed applications up to 800 meters per minute. The RI is the only system that is able to optically verify geometry and color of fiber optic ribbons.
In process the operator will set up the line, including the initialization of the Ribbon Inspector, and then produce the fiber. Whenever the RI detects a defect the images, dimensions and location of the defect are saved to the software database. Any defect that is detected by the system software can send out an alert notifying the operator or integrated PLCs. The defect information and images are available to the operator to investigate if any defect requires corrective action.
Improving Quality Assurance
Suitable for any type of Optical Fiber Ribbon
Since the Ribbon Inspector has uses machine vision, it is able to be used measure the print interval for any shape or fiber count fiber optic ribbon. It is the most accurate and thorough method of measuring ribbon dimensions including width, thickness, planarity, gap distance, and will detect if there is a lump or split defect.
Reduce Frequency of Defects
The system can provide the operator with a view of current ribbon dimensions and color sequence images, along with defect images and current/previous geometry data. This continuous stream of real time information – especially failure data – allows the operator to isolate the causes of ribbon imperfections. Identifying when and how a defect occurs will allow the technical staff to learn the root cause of defects and reduce their occurrences.
Quality Assurance
The Ribbon Inspector system will continuously monitor the geometry and color sequence of the ribbon. The measurements and defect information can be recorded for later analysis. Images of geometry or color sequence defects are captured and saved to a hard disk for use in quality reports. The Ribbon Inspector system’s display makes it easy for engineering and production supervisors to examine potential defects without having to view the defect on the actual ribbon itself. Defect images are saved together with location information allowing your operators to quickly find and eliminate defects before further processing is performed or they fail in the field.
Limitations
There are a few limitations to the Ribbon Inspection system.
- With today’s production lines maximising use of space, installing additional equipment on-line can be a concern. The Ribbon Inspector is able to modify its stand and camera box to best utilize the available spacing, and can even be installed with different orientations to best fit the space.
- • Since the camera is looking at the surface, water droplets/ grease/ dust particles will be affect the geometry of the product and will affect the measurements. Generally, this can be fixed with a well-placed air wipe. Alternatively, the system sensitivity can be decreased, which may result in some of the smaller defects passing through the filter.
Test Results
The fiber Ribbon Inspection system evolved from Taymer’s Surface Inspection series vision systems that detect for surface flaws and measure diameter/widths for round or flat products. In addition the color sequence of the ribbon is able to be measured against a preset template to determine if the ribbon color values change. Taymer vision systems are proven technology and are used to great effect in numerous wire and cable production lines around the world.
Some sample images of detectable ribbon geometry defects can be seen below in Figures 1 and 2. Figure 3 shows detected incorrect color sequence.
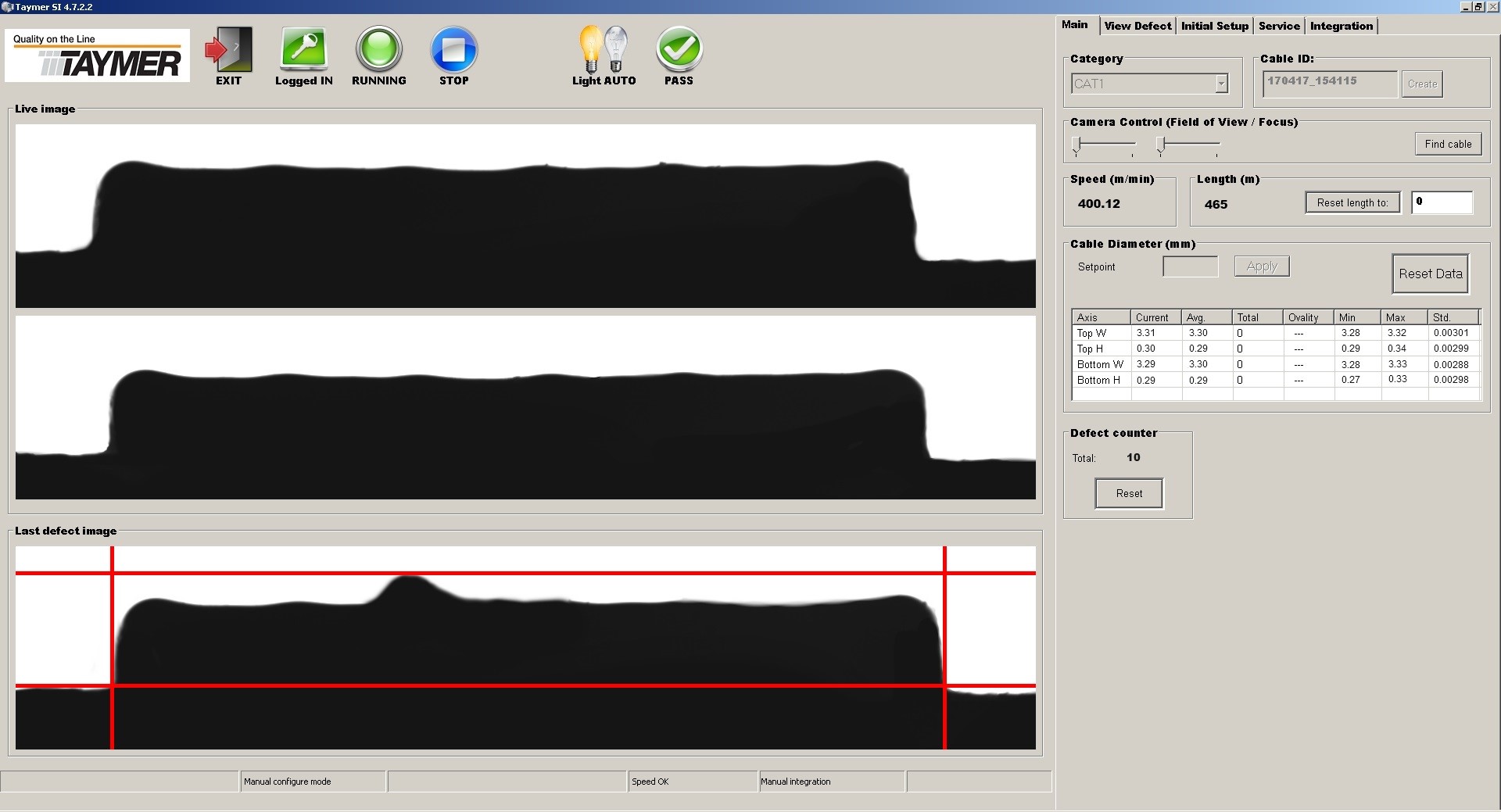
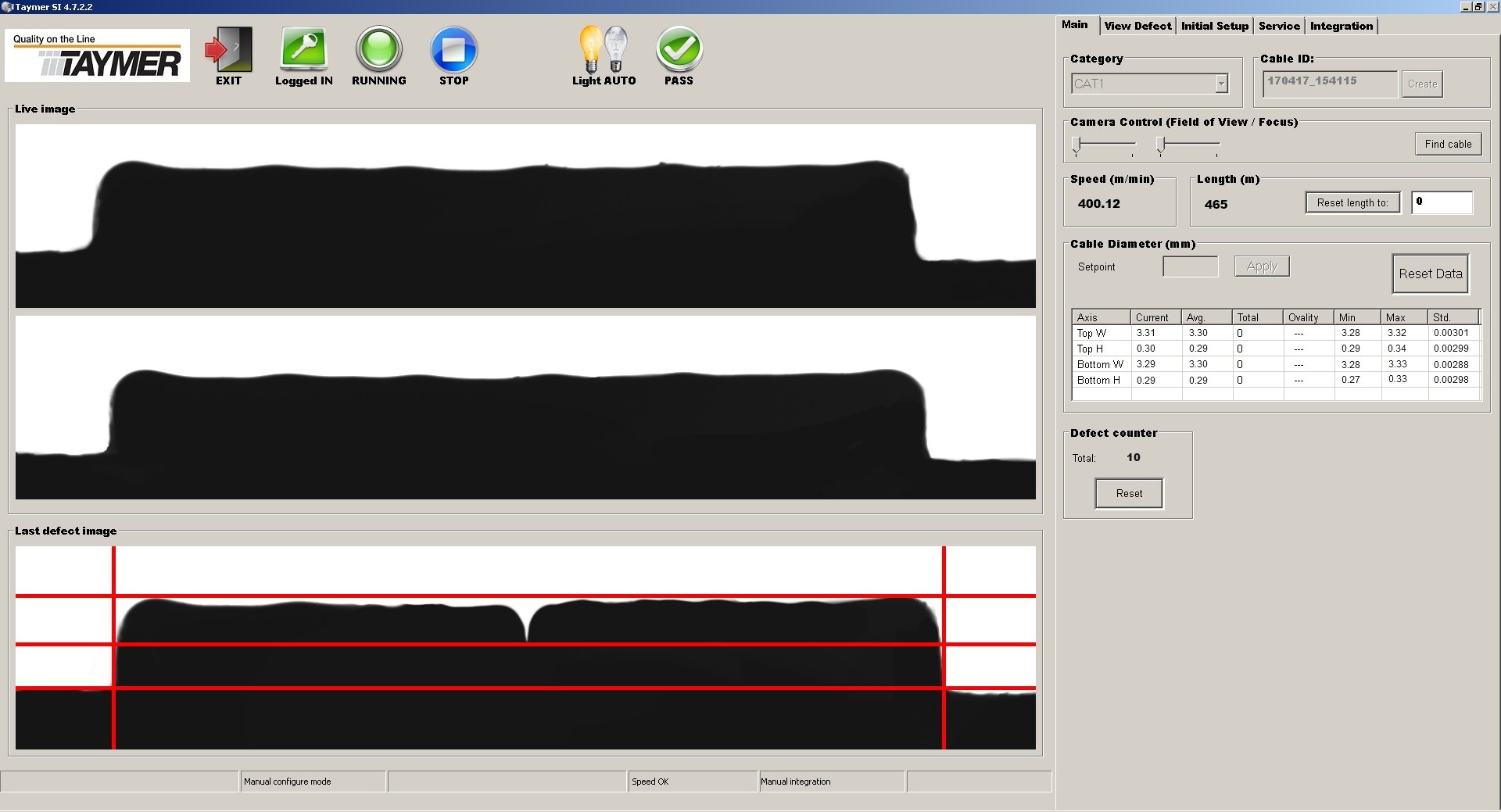
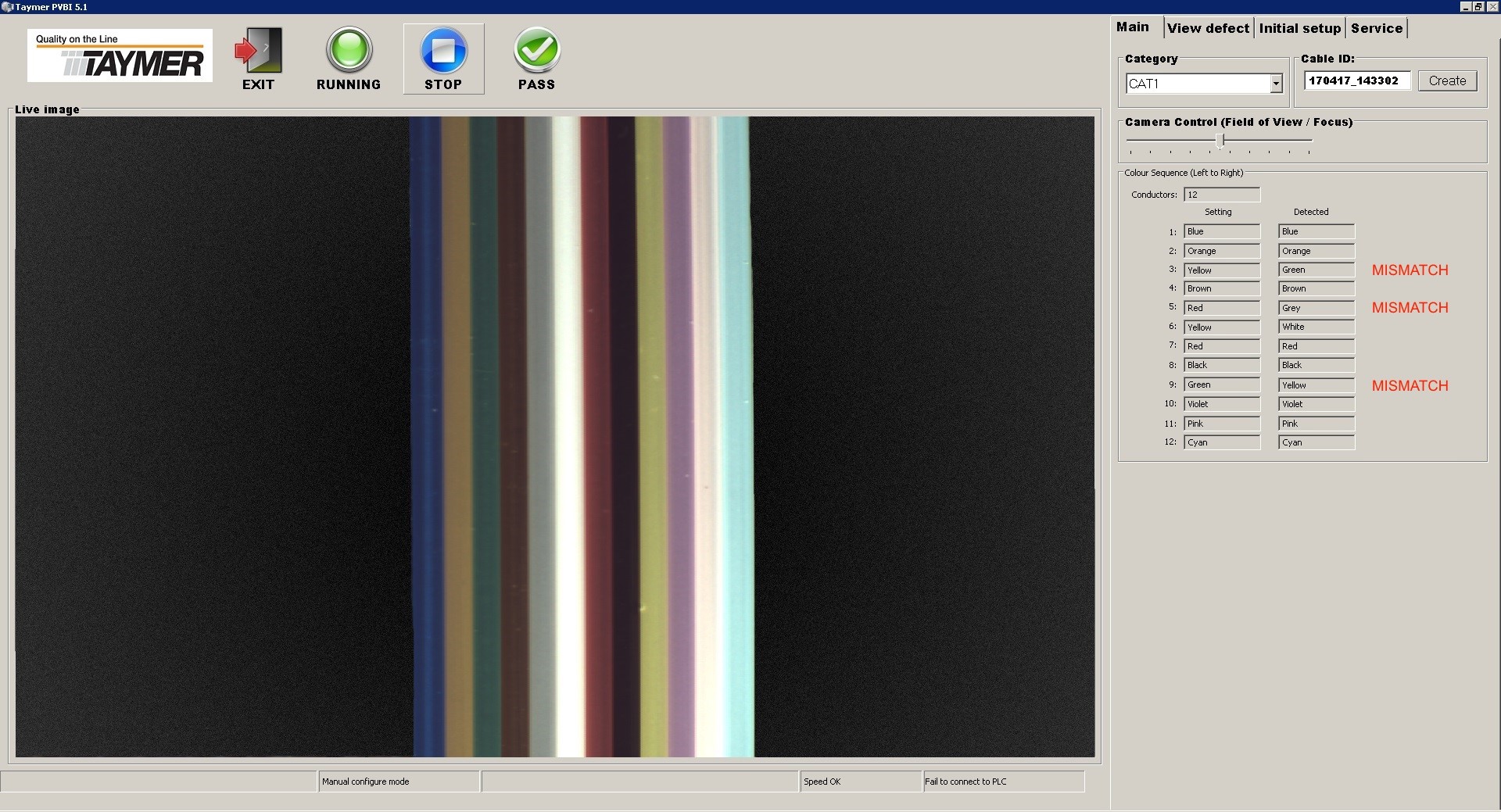
Conclusions
With a fiber Ribbon Inspection system, imperfections in ribbon geometry will be detected and changes in the ribbon color sequence will be caught during production. The system provides several benefits.
- Suitable for any type of fiber optic ribbon
- Works for any number of fiber strand count
- Provides valuable geometry data for use in process
- Ensure defects are found before beginning further processing
- Reduce rework and eliminate cable waste, resulting in significant material and labor cost savings
Contact us today if you would like to discuss Taymer’s Fiber Ribbon Dimensional Measurement and Color Sequence Verification technology further.